How a Photovoltaic System is Built: Operational Phases and Equipment Used
How a Photovoltaic System is Built: Operational Phases and Equipment Used
With the growing focus on renewable energy sources, photovoltaic systems today represent one of the most concrete solutions for producing clean energy, reducing energy dependence, and limiting emissions. However, the construction of a ground-mounted photovoltaic system goes beyond the design phase alone: it requires a complex series of operational steps involving specialized machinery and specific equipment.
From land preparation to module installation, including electrical connections and final testing, every phase of the construction site requires the use of appropriate machines. Alayan offers a wide range of rental solutions capable of efficiently and safely supporting each step of the process, in full compliance with industry standards.
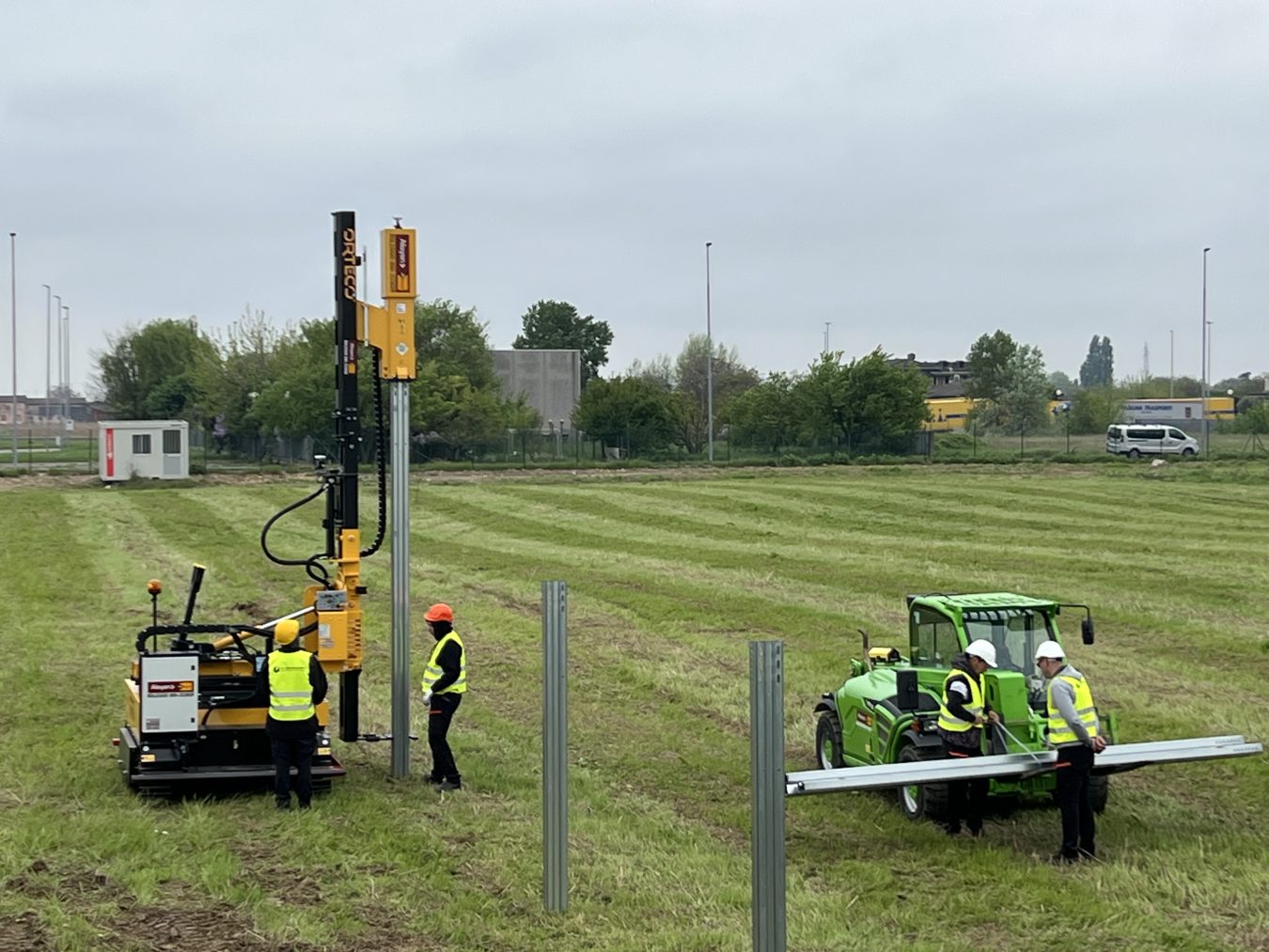
What is a Photovoltaic System?
A photovoltaic system is a setup for generating electricity that harnesses solar radiation through photovoltaic panels. These devices are installed on rooftops, ground surfaces, or dedicated structures, and convert sunlight into electricity via the photovoltaic effect. The energy produced can be used for self-consumption or fed into the electrical grid, making a significant contribution to reducing energy consumption from fossil fuels.
This is a sustainable, efficient, and increasingly widespread technology, offering clear economic and environmental advantages. In addition to reducing CO₂ emissions, it significantly lowers energy bills over the long term.
1. Site Preparation
The first phase involves preparing the ground where the system will be installed. It’s essential to ensure a stable, level surface that is accessible to machinery.
For this task, compact tracked excavators are used, ideal for precise earthmoving even in tight spaces. They are useful for clearing vegetation, digging trenches for electrical cables, and creating holes for fence posts.
In addition to excavators, compact tracked loaders are employed to spread gravel for temporary internal roads and loading zones. With specific attachments like the mixing bucket or forks, they can also mix concrete or move heavy materials such as panels.
The ground is then compacted using a compactor roller, ensuring a uniform level – crucial in large-scale solar parks.
Temporary fencing like Orsogrill barriers is usually installed to safely demarcate the area, and construction containers are often set up to serve as mobile offices or dressing rooms for technical staff.
2. Installation of Support Structures
Once the area is prepared, the metal frames that will support the panels are installed. The key machine here is the tracked pile driver, essential for quickly and accurately driving steel poles into the ground. It ensures maximum stability, even in high winds or poorly compacted soil.
If the ground is very hard or rocky, augers may be required to drill deep holes for concrete footings.
In such cases, the mixing bucket for the skid loader is used to prepare the necessary concrete directly on-site, ensuring continuity of work.
3. Installation of Photovoltaic Panels
The next step is installing the photovoltaic modules. This is a delicate phase requiring precision and safety.
Panels are typically delivered by truck and must be unloaded and moved on-site. For this, off-road telehandlers are used, such as the 20 q model or the 90 q model. These machines allow access to central rows without compromising load stability.
Once the modules are in place near the frames, they are fastened. Operators work at height using scissor lifts, which provide a stable, safe platform, reducing fall risk and improving installation efficiency.
To optimize on-site logistics, equipped vans are essential for transporting tools, small parts, and accessories, keeping everything organized and protected.
4. Wiring and Electrical Connections
After placing the panels, the electrical connection phase begins. This involves connecting the modules and routing the power to the inverter and grid connection point.
During this phase, narrow-bucket excavators may be used to dig small trenches for underground cables, minimizing environmental impact and speeding up ground restoration.
In large systems, cable laying machines or cable reels may also be used to ensure neat, safe cable runs.
5. Testing and Final Touches
The final phase includes functional testing and site finishing. In low-light or nighttime operations, mobile lighting towers powered by diesel or electricity become essential. These may require standalone generators when using electric models, ensuring consistent lighting in operational zones.
Until the system is fully commissioned and connected to the grid, diesel generators may be used to temporarily power test instruments.
For final checks and site supervision, pickup trucks are a fast and practical solution for moving efficiently across large areas.
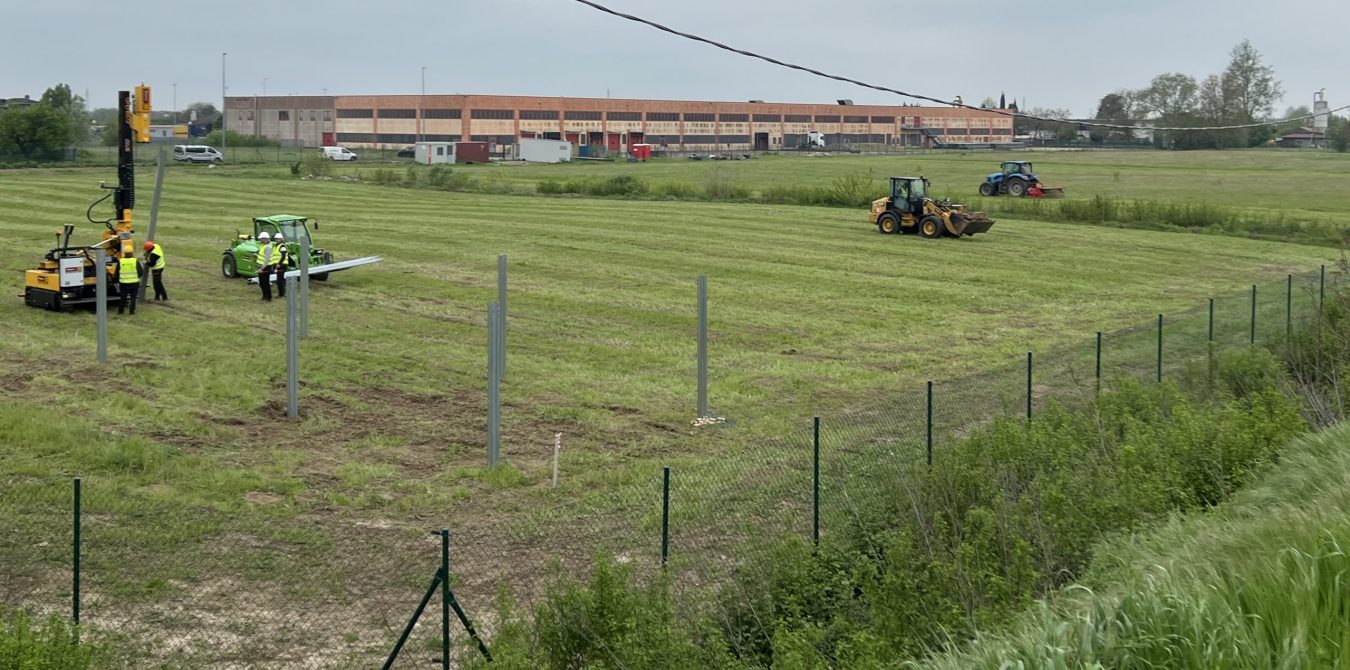
Conclusion
The construction of a ground-mounted photovoltaic system requires experience, planning, and specialized equipment. Choosing to rent professional machines from reliable partners like Alayan means having access to modern, versatile, and ready-to-use solutions for every phase of the project, from earthworks to final testing.